Meet the designers- Lynton Pepper in London
Lynton and Opendesk go back a long way. In fact, the relationship goes back further than Opendesk itself, to Architecture 00, the practice from which Wikihouse and Opendesk have grown. Lynton, part of the founding team at 00, spent many years working alongside our very own Nick Ierodiaconou and Joni Steiner. His designs, the Pedestal and Wikibooth, have been mainstays in the collection for some time. We caught up with Lynton at his home in East London.
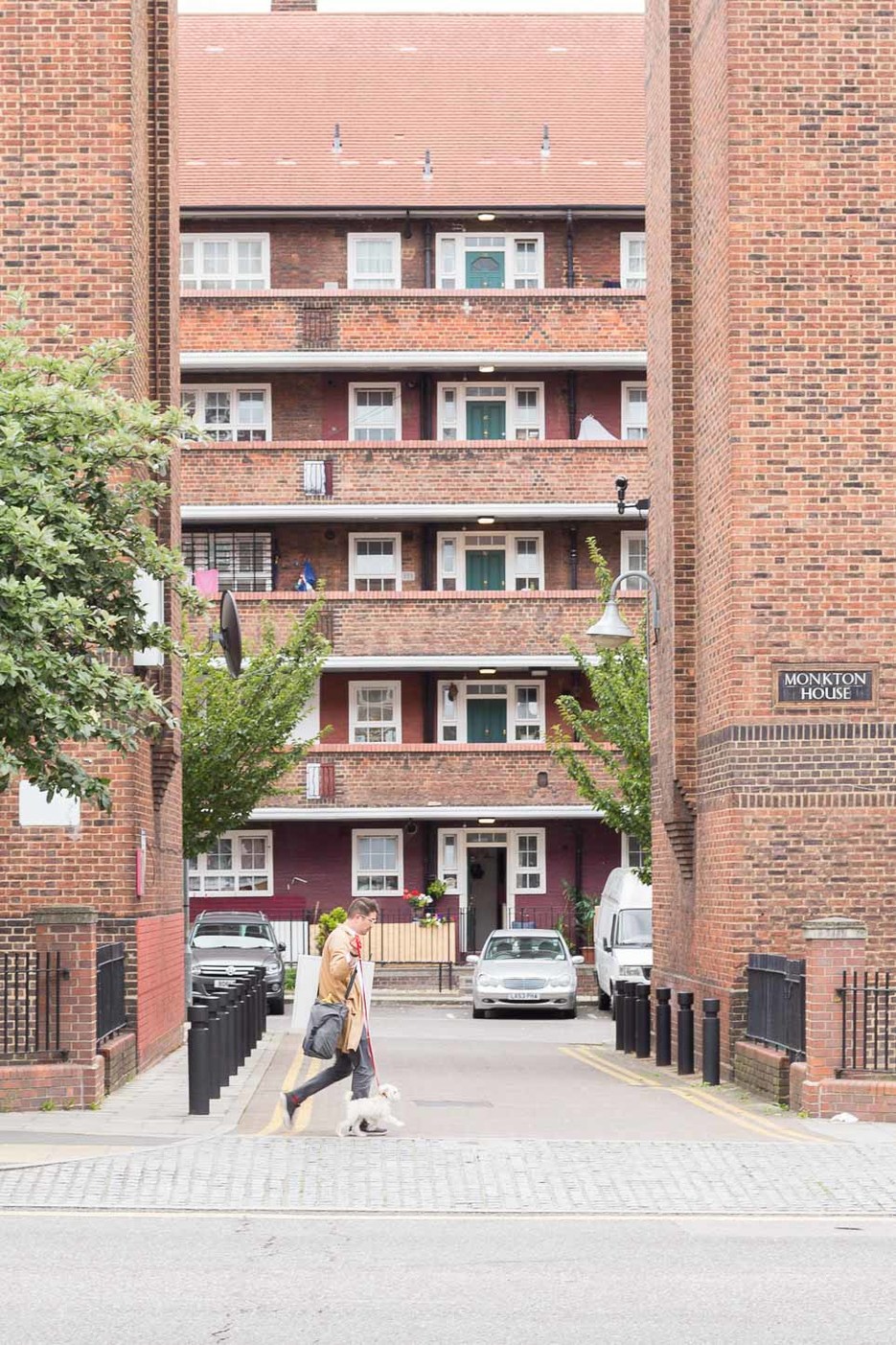
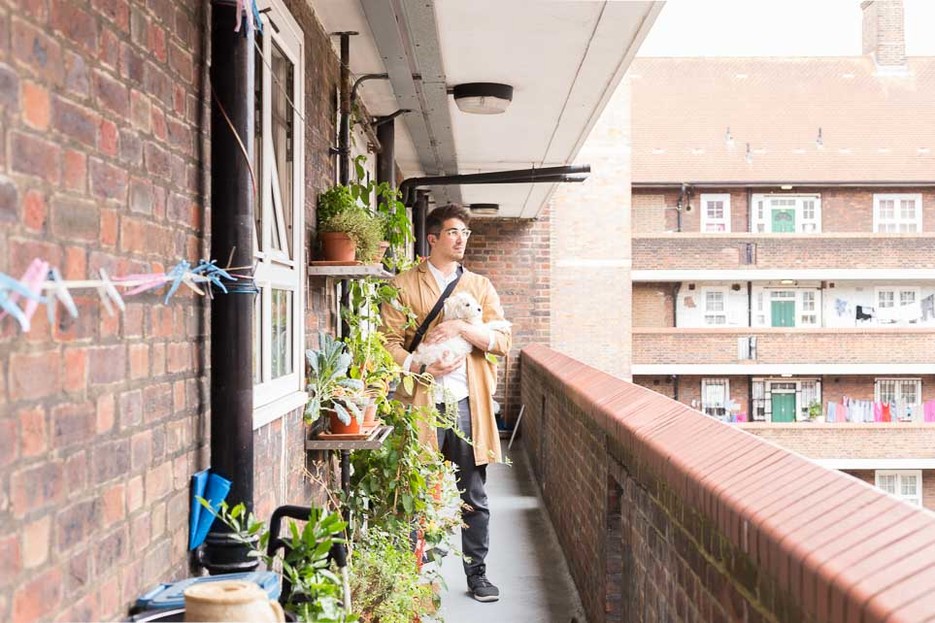
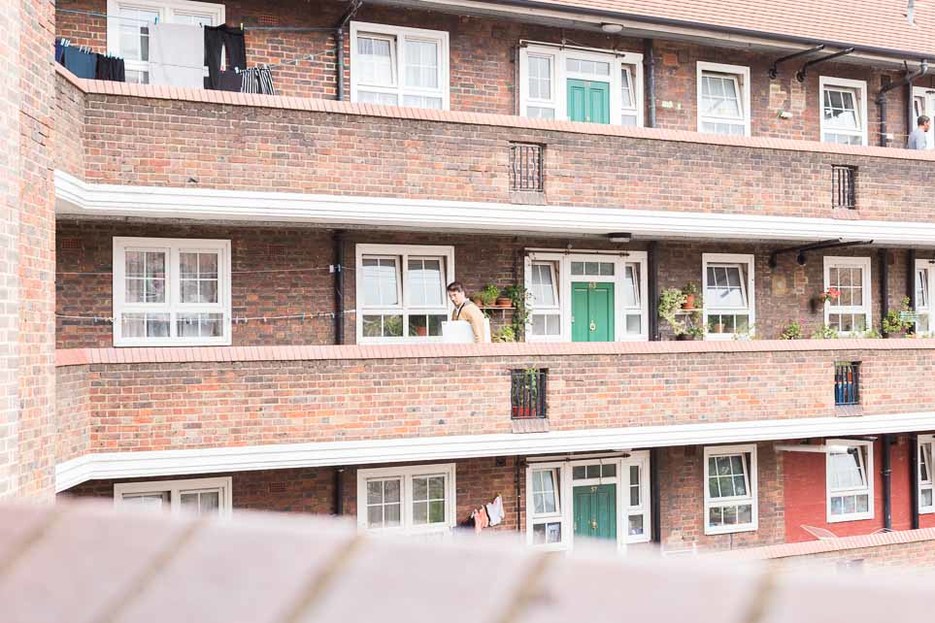
Opendesk: Introduce yourself! Give us a brief history of you from your days at school to now. How have you ended up where you are?
Lynton: I went to secondary school at the Royal Grammar School in High Wycombe where I studied my favourite subjects for A Levels – Art, Physics, and Maths. High Wycombe itself is famous for its furniture making with the likes of Ercol being based there, and ever since my first visit to the Chair Museum I’ve always wanted to live in the woods and be a Bodger. The idea of being able to create something that can improve life through design has always interested me.
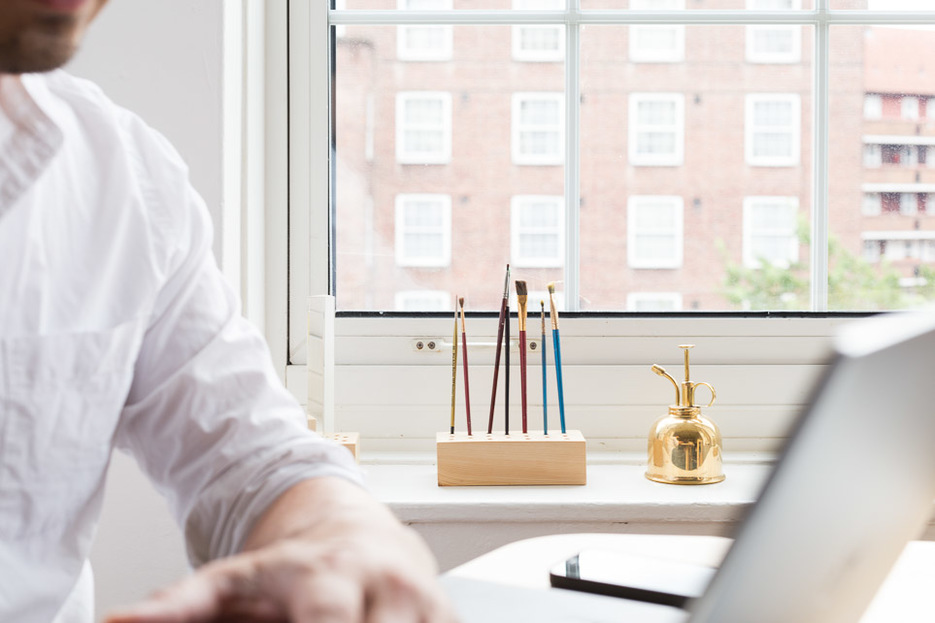
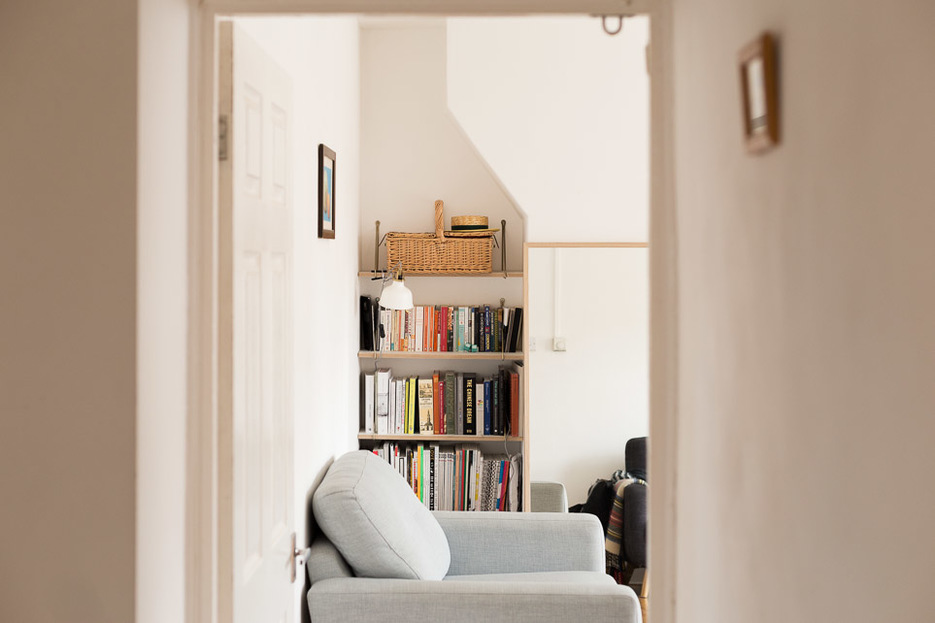
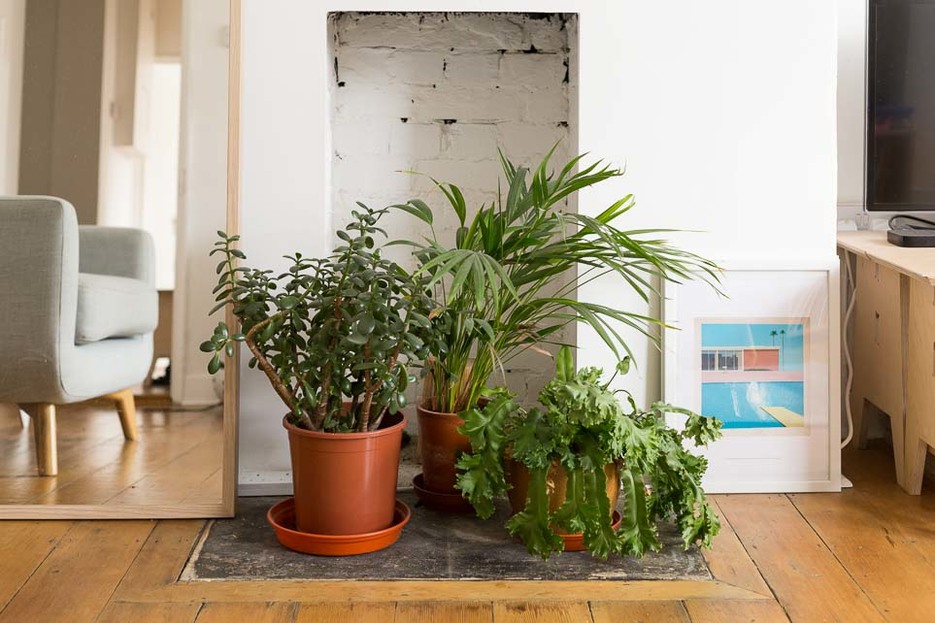
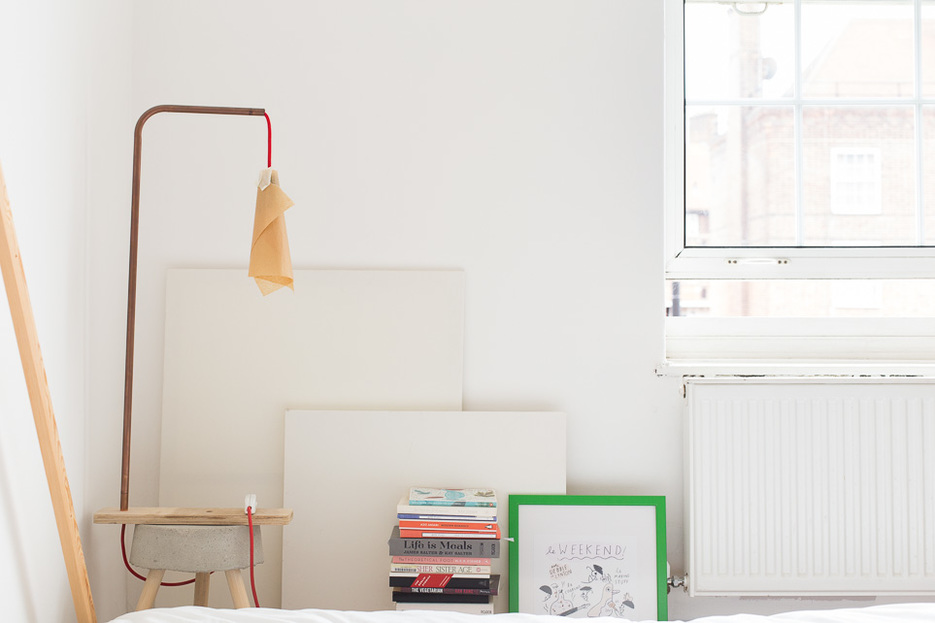
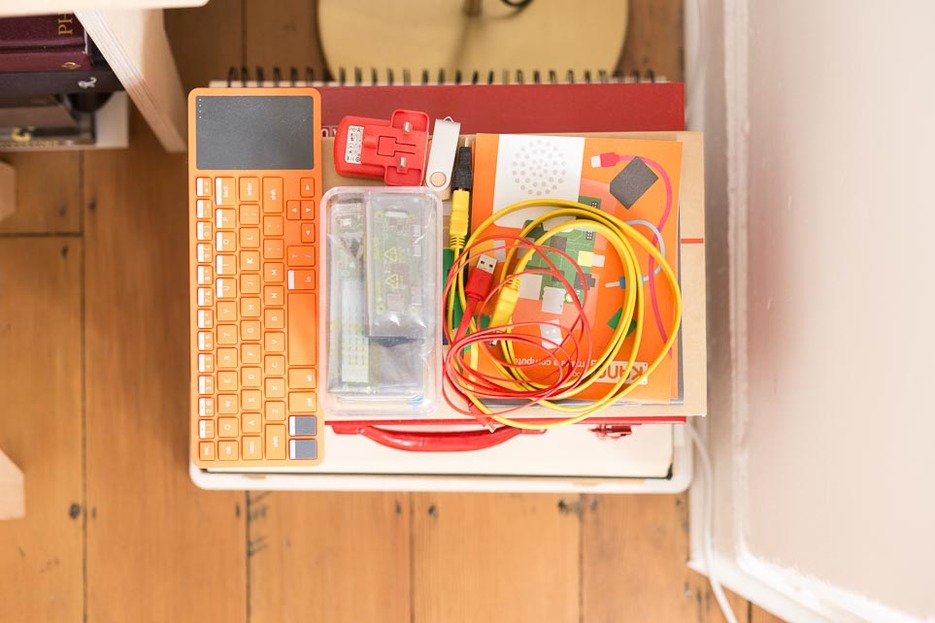
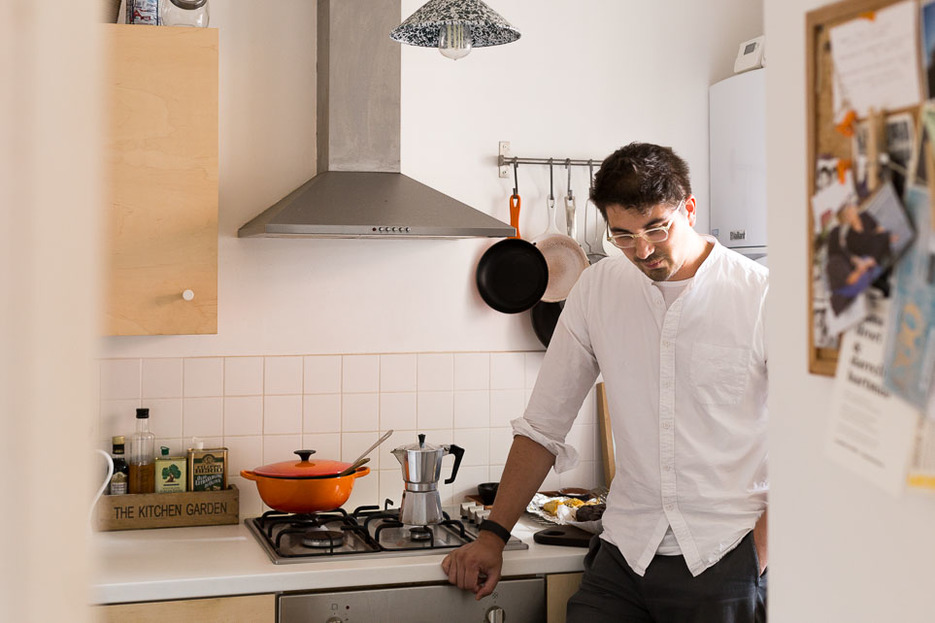
“ever since my first visit to the Chair Museum I’ve always wanted to live in the woods and be a Bodger.”
Lynton Pepper
I went on to study Architecture at the University of Bath where we were encouraged to critically resolve a brief through design, but also observe and identify problems in the world around us. This is where my interest in coercive design developed and has been a part of my work ever since, be it in buildings or furniture. People usually follow the path of least resistance and therefore any behaviour we wish to promote must be designed in a way that it is the easier thing to do.
After finishing university, I worked at an architecture practice specialising in sustainable design, whilst simultaneously working on the very first projects at Architecture 00 in the evenings. Once we had enough work, we officially formed the practice. We wanted the organisation to afford freedoms, allowing people to explore and experiment with new ideas. Opendesk and Wikihouse are two of the better-known experiments.
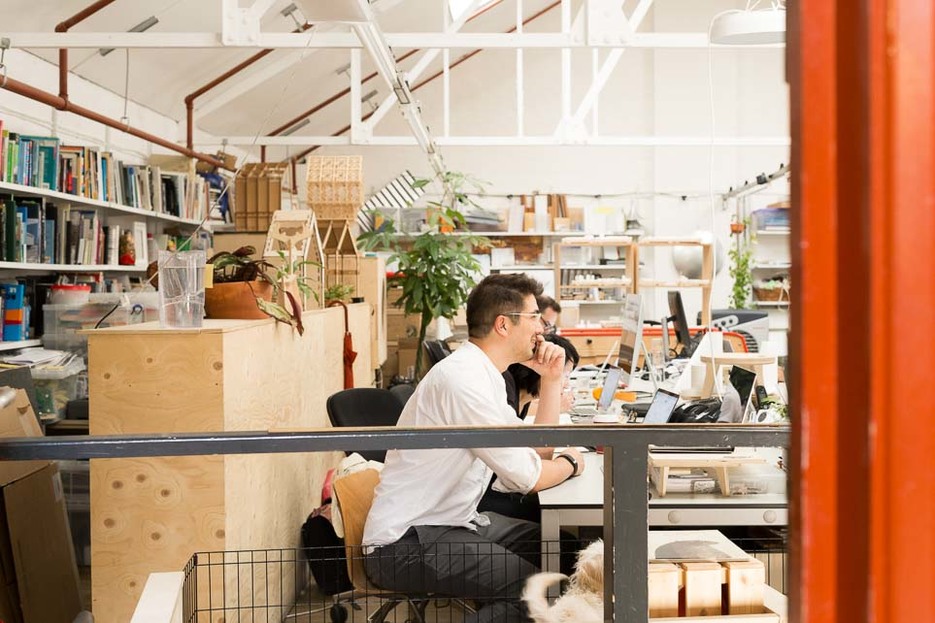
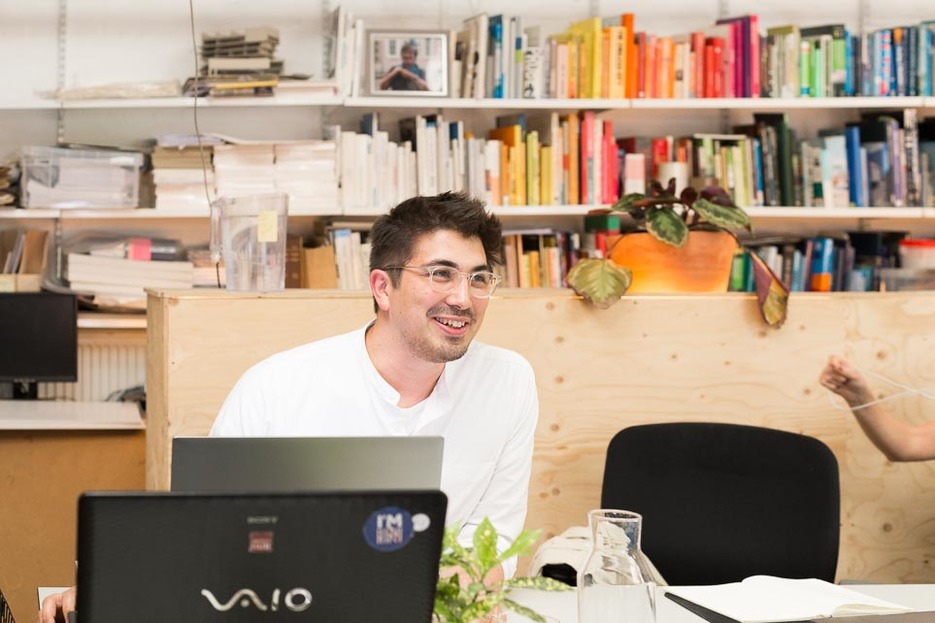
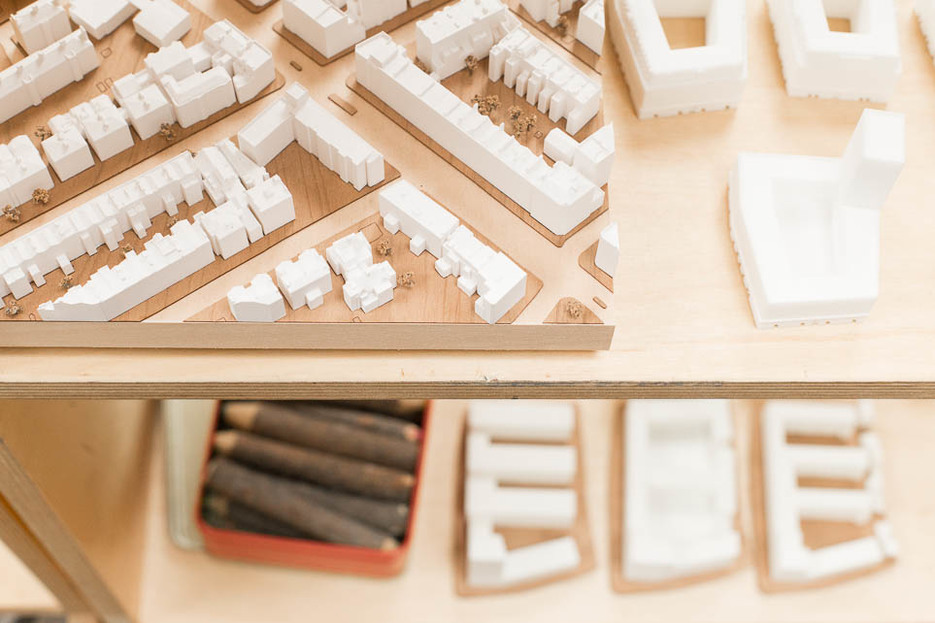
Architecture 00 is a practice with a track record in delivering a broad range of activities relating to the shaping of our built environment. Founded in 2005 by a group including Joni and Lynton, 00 office’s brings together skills in action-led research, urban design strategy, architecture and place making with a detailed understanding of how the physical fabric of buildings can be accompanied by innovative, engaging and collaborative processes.
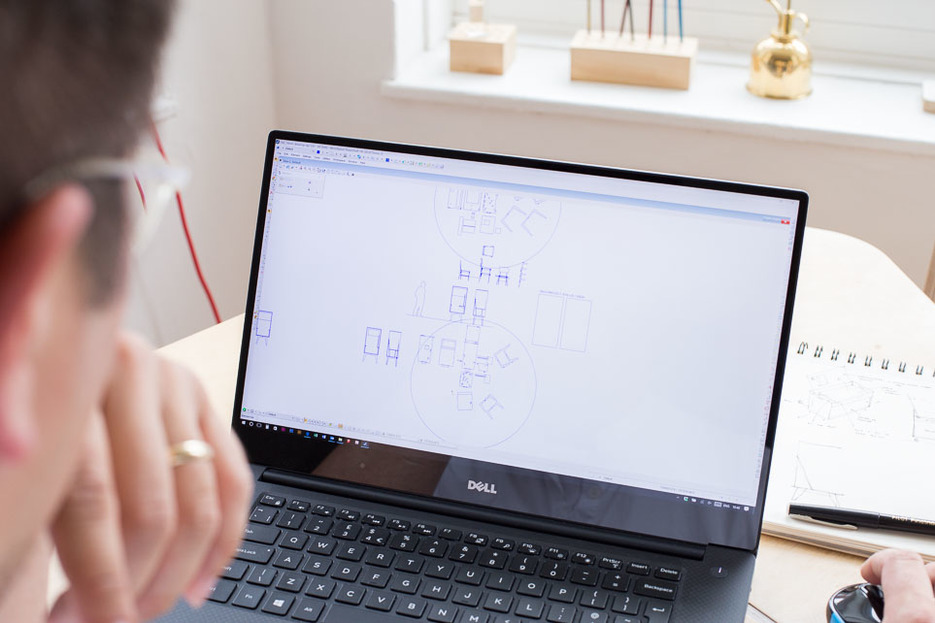
Opendesk: Tell us about your design approach when working with CNC fabrication.
Lynton: I typically design in 2D and rarely use 3D CAD software, partly for the mental challenge, but also because I feel that I have more control over the design. It’s also true to the process for which I am designing - an 8’x4’ sheet of plywood and a CNC machine is in principle very similar to a sheet of paper and a pencil. Designing in 2D also helps me visualise how something will be cut through knowing I will only be using one-sided cutting, or that you can fit multiple designs onto one sheet.
Material efficiency is very important to me as it affects cost so much. I spend a lot of time figuring out the best, most efficient nesting solution for my designs (how the parts fit onto a sheet of 8’x4’ plywood). I also enjoy designing objects that can be made entirely from one material and process so I avoid the use of complex hardware and instead come up with simple CNC made hinges and fixings.
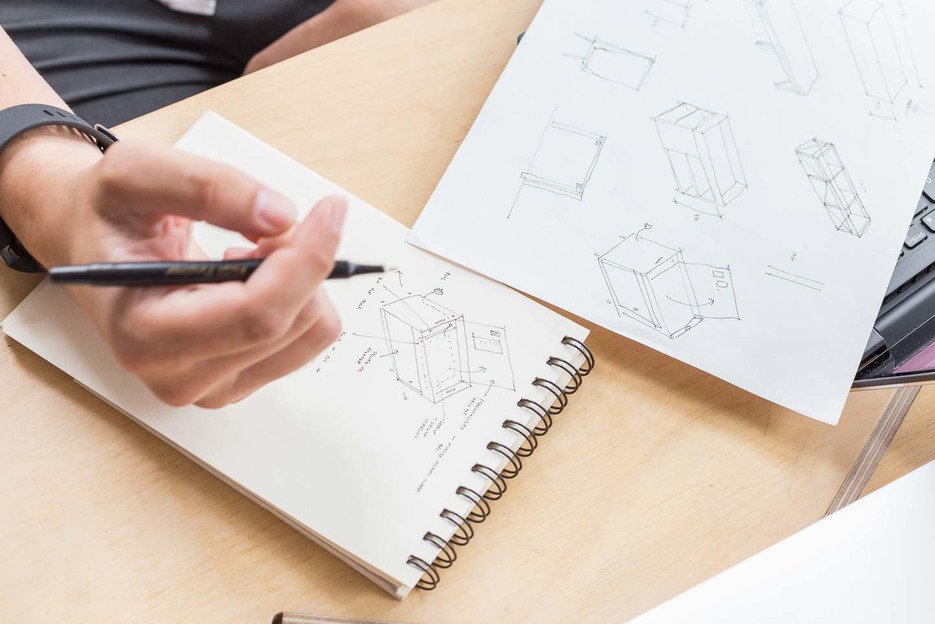
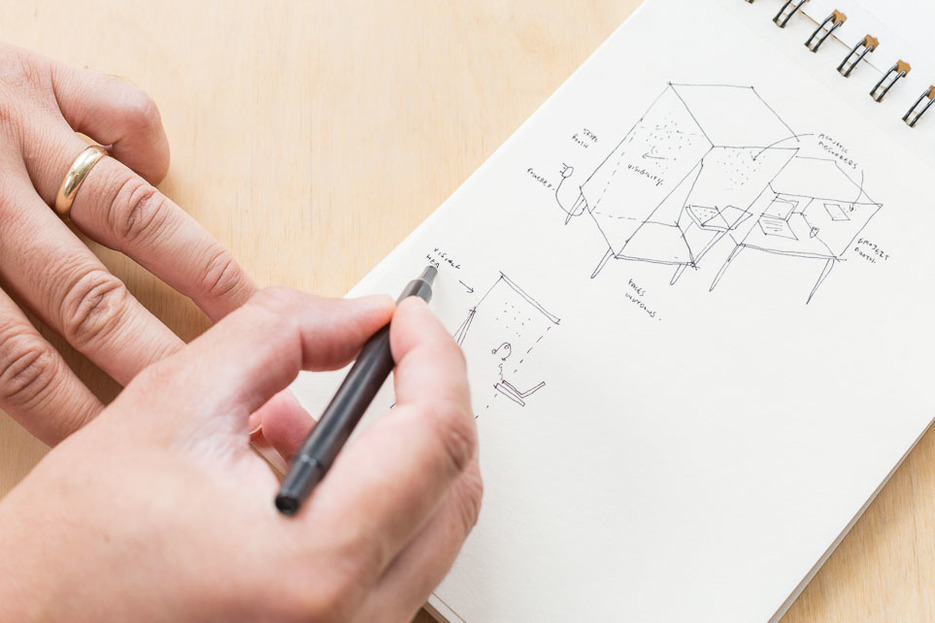
Opendesk: How did you become involved with Opendesk?
Lynton: Since we were at university together, Joni has always been interested in furniture fabrication. He introduced me to CNC machines many years ago. This opened my eyes to the possibility of customisation that would enable functions that simply did not exist yet. Digital fabrication tools allow great freedom. One day you can be cutting a piece of furniture and the next day a full-size house. All this without the cost of tool or mould changes commonly seen in conventional mass manufacture.
This concept came to fruition in the Hub Westminster co-working space project in central London (an Architecture 00 project) where we designed all the furniture to encourage people to work collaboratively and allow the space to be reconfigured in minutes. The initial plans for the Hub had a CNC milling room to enable furniture to be customised within a few hours.
This extraordinary freedom of being able to identify a problem and design a solution which could be prototyped in a few days means that we use CNC milled furniture in pretty much every architecture project we do at 00.
Opendesk: Tell us about your own views of Open Design and distributed making. Why does the topic interest you?
Lynton: I’m fascinated by the democratisation of design. The tools and resources to create anything and everything are more accessible than ever. Open Design gives people the understanding that they can adapt the world to suit them instead of having to make do with what is given to them. This is an empowering freedom, one that empowers me in my own design work. For this very reason all my designs are Open Source and I hope that others can be inspired to learn and eventually participate in Open Design in the same way I was.
It’s also important to me that my designs are cost effective and simple so they are accessible for anyone wishing to make them. I try to keep all my cutting files efficient, requiring only single sided machining. I also avoid screws and other hardware that may be unavailable in some parts of the world.
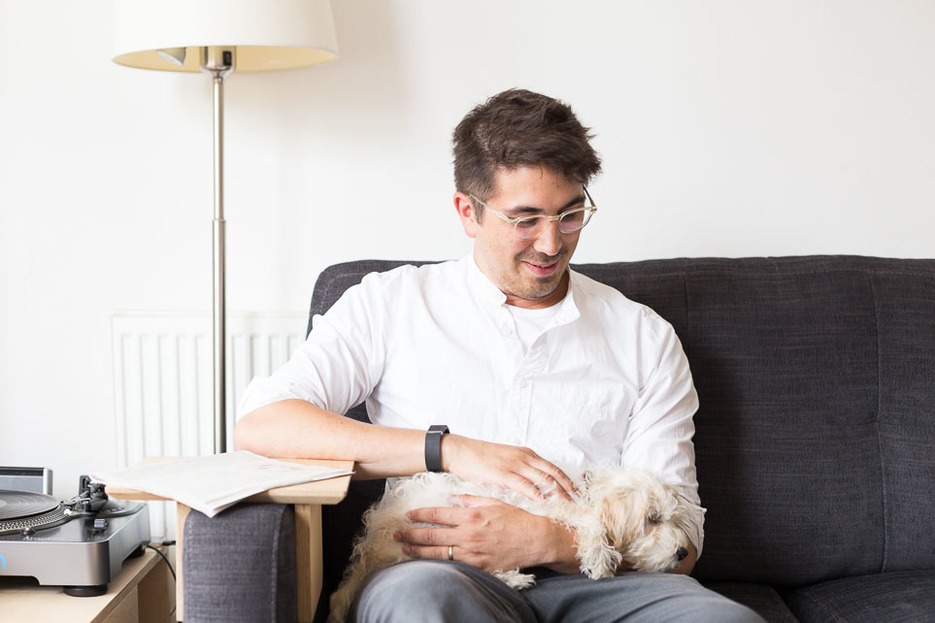
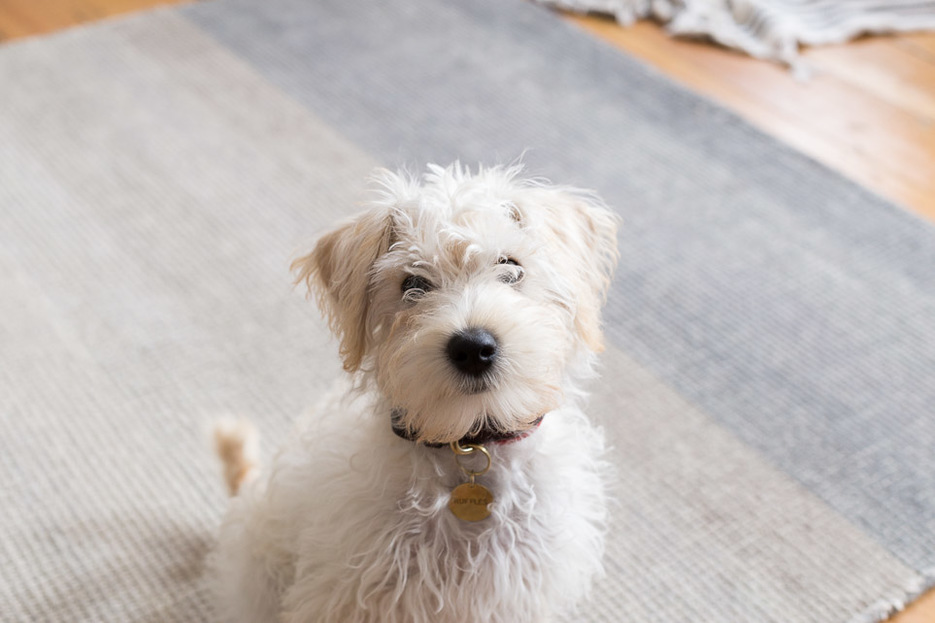
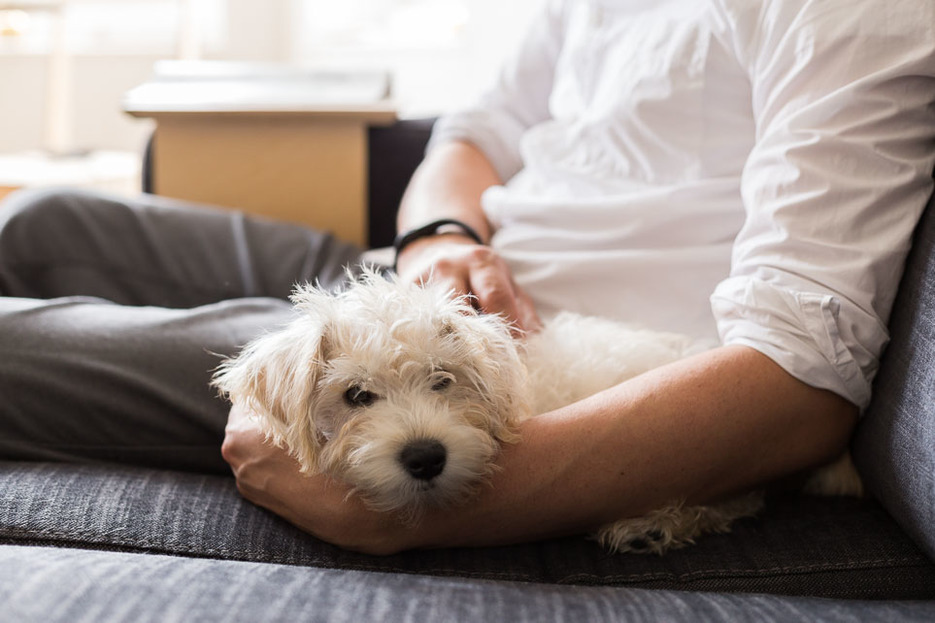
Opendesk: Got any personal design projects on the go? Also, you’ve got to introduce us to Jake!
Lynton: I’m always designing bits of furniture or items that we need in our new unfurnished house. Being able to knock up a bespoke solution to any problem we have has been super useful. The new design challenge is our puppy, Jake, and finding out what he would like in his new home. I think we will be making a dog house with a viewing platform so as he can look out of the living room window.
“Knowing how things work is such a liberating factor in life.”
Lynton Pepper
I also enjoy a good Wikihouse build. It is so satisfying to assemble such a large scale object with friends. It is a perfect example of democratising design as you suddenly understand how things work, empowering you to make your environment how you want it to be. Knowing how things work is such a liberating factor in life.
My other hobby is fashion photography. Architecture is brilliant but it is such a long process taking months, often years to complete projects. I really enjoy the fact that I can do a shoot in an hour with some delightful people and create something amazing in a short space of time. It’s a similar enjoyment to designing furniture for digital fabrication tools in that it is so quick to do.
Photography by Josh Worley